“Retrofit” – There is much to do!
I’ve been chatting to Victoria Evans and Lee Boileau and I’m feeling a little overwhelmed….

Sustainable is the current buzz word and climate change is an increasingly hot topic (pardon the pun). The challenges that lie ahead seem just enormous and absolutely everyone has a role to play. We all, by now, know something of renewable energy; ground source and air source heat pumps, photovoltaics and sustainable material choices, but there is so much more to it when it comes to the built environment and the role that the construction industry has to play.
The Government has long been working on a blueprint that initially required all landlords to upgrade their properties to reach a level of sustainability in order to let or sell them and to move us all off fossil fuels by 2050. Potentially this would have affected every landlord in the country (85% of stock would have been affected) and UKGBC estimated in 2020 that, in order to hit this target, 1.7 houses would need to be completed every minute for the next 30 years. That was quite the challenge and the Government has just redacted this obligation for Landlords to meet certain EPC targets. Nonetheless, there is still clearly much to be done.
Victoria, Managing Director of Castellum began by acknowledging the country’s carbon targets (80% emission reduction by 2050). “We all have a responsibility to transform the built environment. We are actively preparing our business for the future by combining our luxury residential build experience with expertise in the application of successful retrofit across all our locations and we are committed to investing in our team to help enable this.”
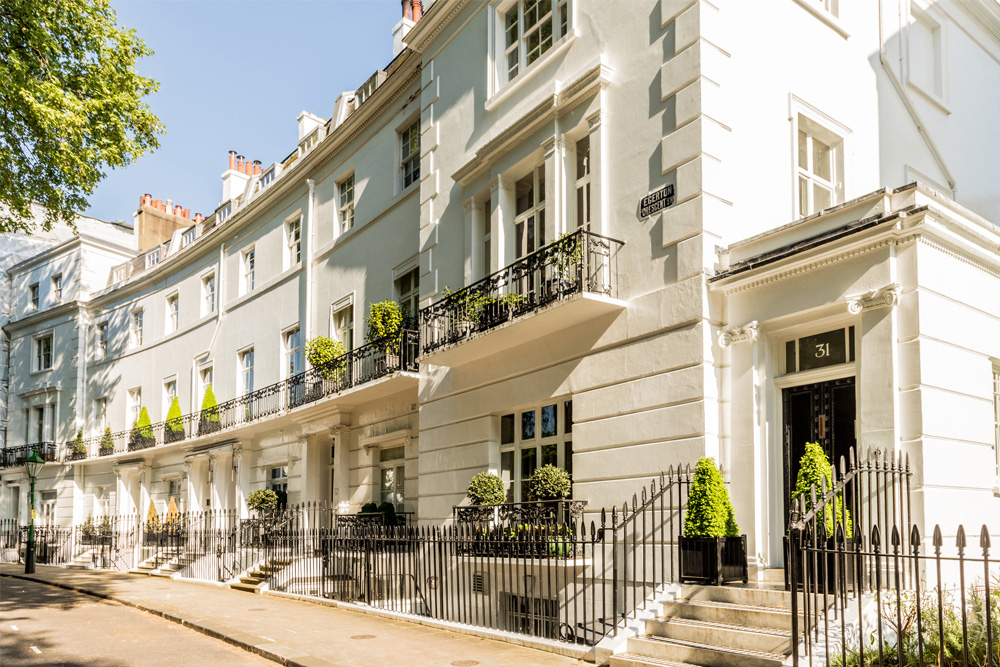
It is an unusual step for a Main Contractor to become a Retrofit Co-ordinator and I went on to speak to Lee Boileau, Project Director for Castellum in London and our first qualified team member. I was keen to find out what it all means and why it was so important to the business. Retrofit Co-ordinators manage the PAS 2035 process which is the British Standard that sets the framework that the Government are working towards. It is complex and an incredibly ambitious target with, frankly, a terrifying amount of work to be done. Fundamentally though (and before I fall too far down that particular rabbit hole), retrofit is based on the whole house approach which always starts with surveys and repairs/maintenance of the existing structure. The key to it all is getting the building envelope right before any internal upgrades begin. Once that hurdle has been cleared, in addition to ensuring that every home is no longer powered by fossil fuels and runs solely on renewable energy, there are six key building physics principles required and included in the PAS 2035 framework:
-
Insulate (floors, walls, roofs)
-
Windows (install good efficient ones)
-
Ventilate (with heat recovery, MVHR best)
-
Make airtight (tape all external fabric junctions)
-
Thermal bridges (identify and address them)
-
Moisture (make sure there are no risks of condensation & understand water vapour)
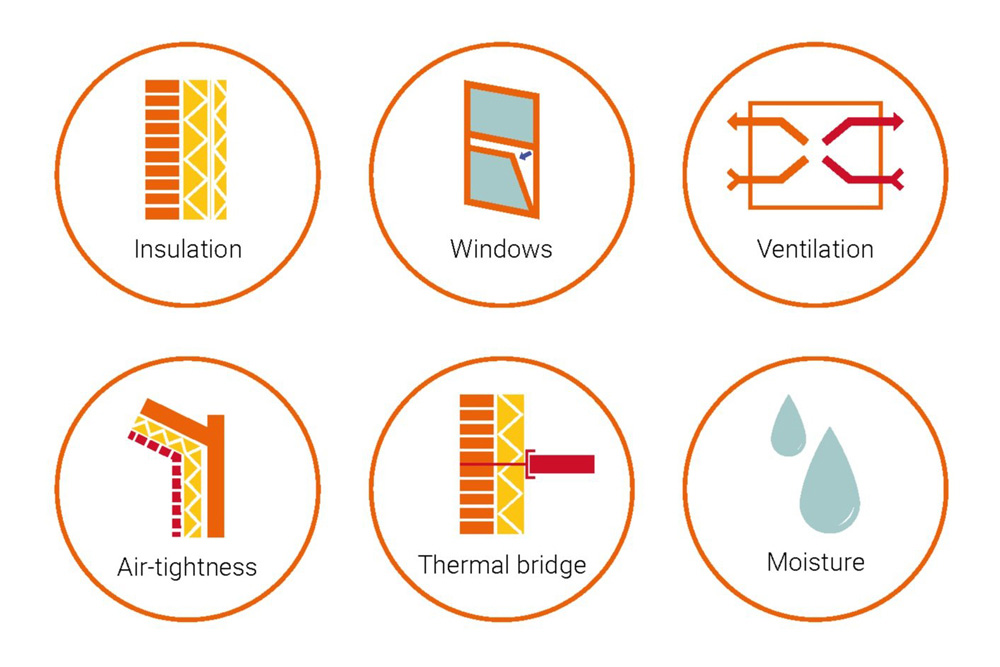
Six key principles of Retrofitting – StudioPDP
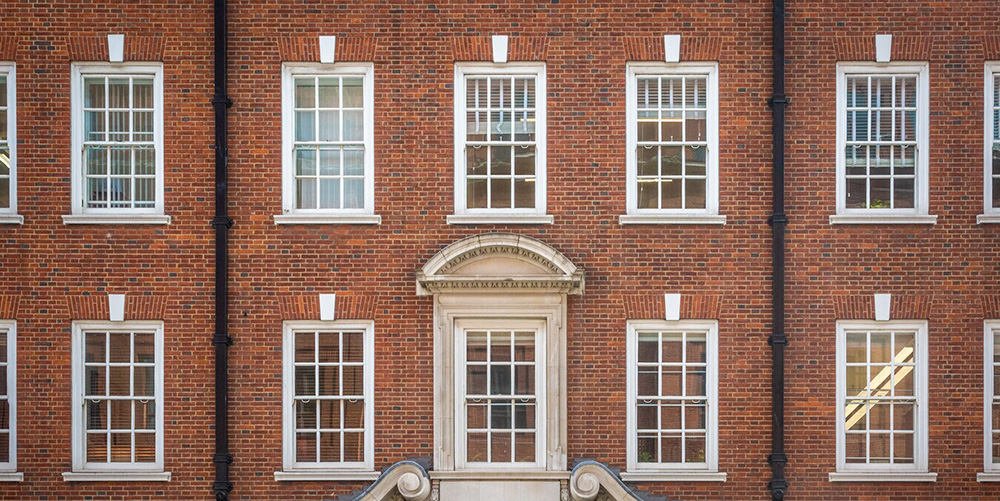
I suppose that sounds simple enough but the reality is far from it, especially when you consider that few of the new houses being built today meet all of the 6 principles (why is that?). Next you need to know that only about a quarter of our housing stock is post 1980 – most really is quite old. We have over 27million homes in the UK, spanning centuries; about 2% of the stock is listed and we have over 10,000 Conservation Areas; this building stock is all protected by Historic England. One should also bear in mind that, whilst often extremely beautiful, old buildings are becoming increasing unappealing to home owners due to their energy inefficiencies coupled with soaring bills, lack of comfort and ongoing maintenance requirements. These houses were designed and built for a lifestyle and comfort levels that is almost unrecognisable today. Open fires have been replaced by central heating and electricity has replaced candles. People spend more time indoors (and over half of the UKs household now have pets).
Multiple hot baths and showers per household, per day, are now the norm. We use multiple heat generating appliances that did not exist when many of these properties were built and, did you know that each person breathes out about half a pint of water into the air each night? I didn’t quite believe Lee when he told me that (it wouldn’t be the first time that he had pulled my leg) but I checked and it is true! What happens to all of this increased moisture, particularly given the requirement to make properties airtight? This makes my mind boggle a little…
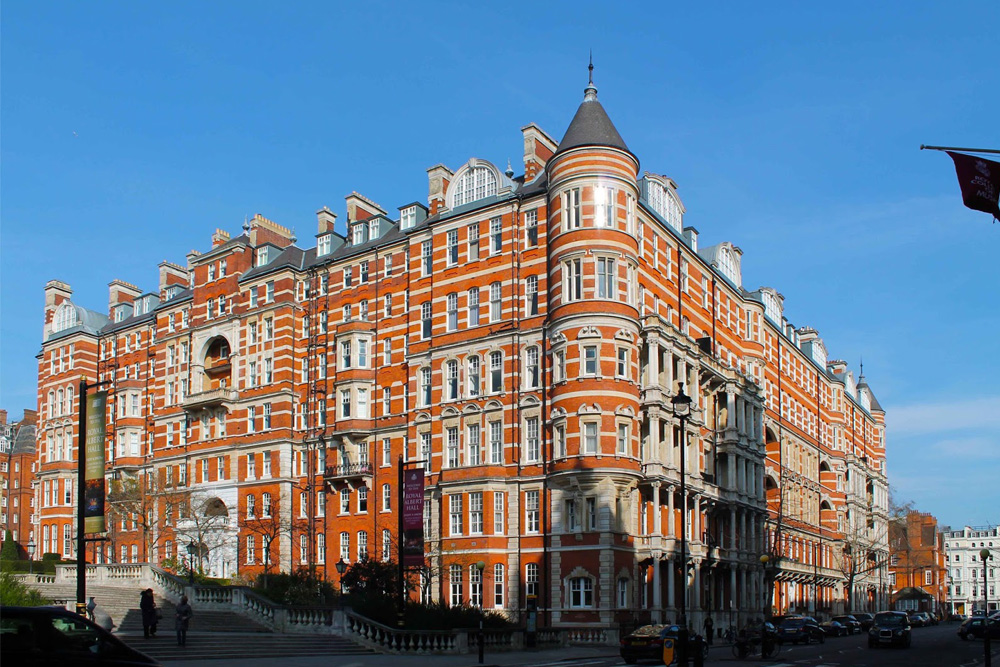
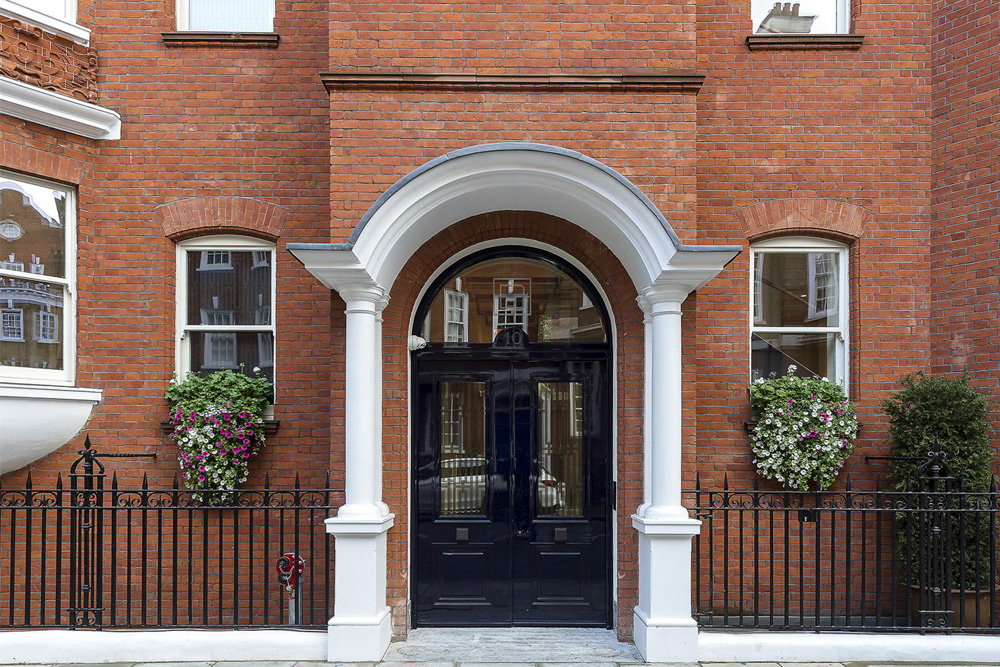
The new technologies involved are many and varied. Lee talks me through a new breathable product called Diathonite – it is a lime and cork insulating plaster that is sprayed on in layers. It is applied in 25mm thick layers and 50mm takes a month to dry. A month! It can be used internally or externally to the external walls of a house and, in order to be effective internally it has to wrap around the soffits and slab with joints being taped to make them airtight. It cannot butt up against regular plaster which it reacts with so it requires specialist joints but you can use the top coat on the other internal walls which is good as it has a slightly different texture to regular plaster.
There are very few contractors using this product as yet and it has to be used in combination with a robust airtightness strategy that gets tested at every stage to ensure the project is draft free and able to keep the warmth in. It is, as you might imagine, very expensive at the moment. Finally, it needs to be finished in a breathable paint like Graphenstone – if you haven’t come across Graphenstone paint by the way, look it up… they offer a range of beautiful colours and it ticks all the sustainability boxes.
Aerogel is another recently developed breathable (vapour open) material that apparently can be applied so thinly that original cornices and mouldings are not affected as it is the lightest solid material known and the most efficient; initially developed by Nasa for use in space missions.
Air source heat pump technology is also progressing and you can now get units that will sit on top of roofs, with separately metred splitters meaning that one pump can serve multiple apartments. Secondary glazing has also moved on significantly and upgrading windows is usually a relatively easy win, though again, this might not be possible on a listed building or one in a Conservation Area. New products such as vacuum glass – which looks like single glass but performs as triple glazing are helping insulating buildings whilst meeting energy efficiency requirements without compromising on aesthetics. Historic properties are far, far more complex than new build but most measures are possible and where you cannot do everything, you may have to ramp up other elements to compensate or plan a stage by stage approach.
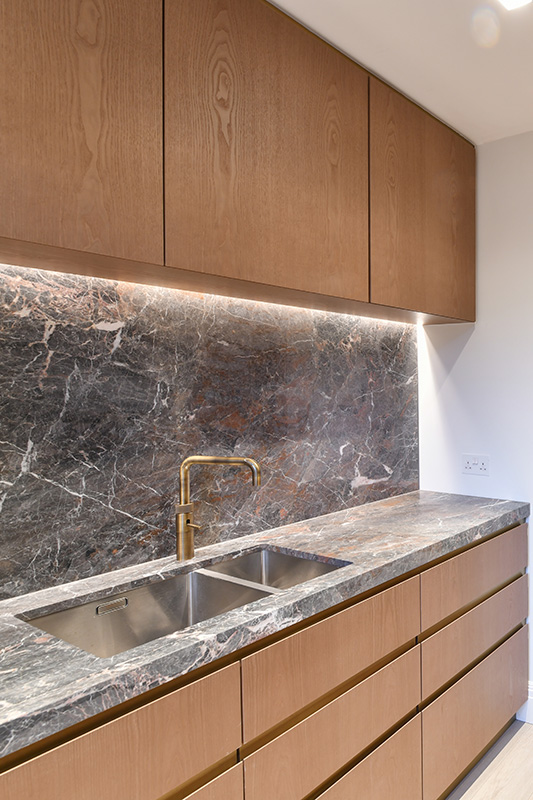
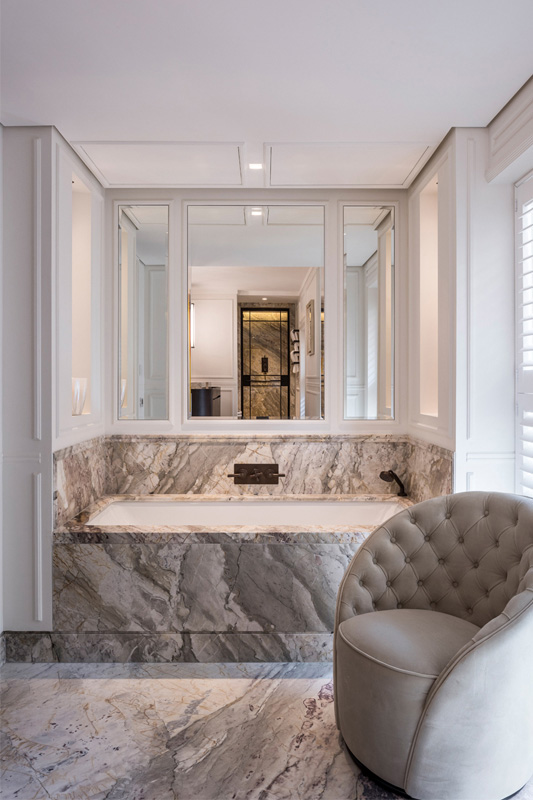
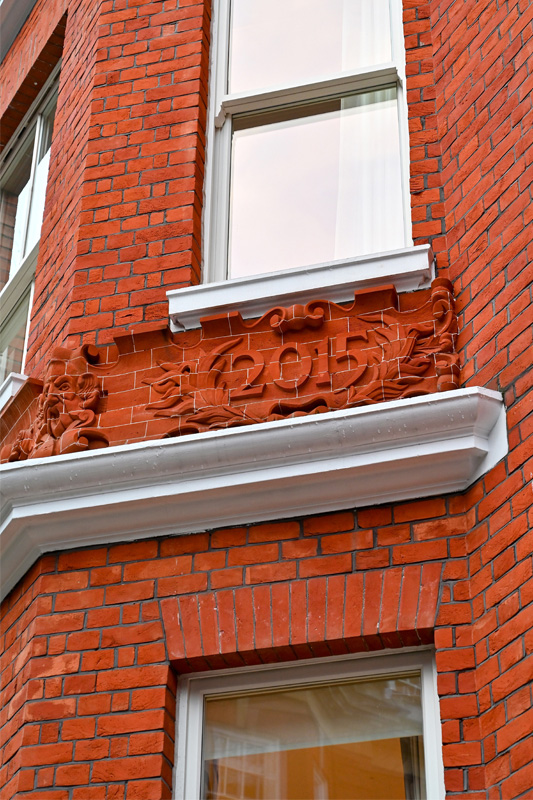
Part of the retrofit process is to understand who will be living in each dwelling and tailoring the updates to that building for maximum effect. External defects must be taken care of first, all drafts and gaps to be closed-up and ventilation system to be installed, then an MEP system needs to be designed and insulation to be specified in combination, as the two work hand in hand. At this point remember that you cannot clad the facades of historic buildings and so for these properties, all insulation improvements must be done internally and that is not always possible or quite complex if there is historical panelling, or detailed cornicing involved. A close relationship with conservation officers is highly beneficial to help negotiate your way through these upgrades.
Gaps must be sealed and, if you are sealing gaps you must then introduce ventilation. I know – it sounds bonkers doesn’t it? But a controlled ventilation will be critical in purging all the moist air our of your house, best fitted in the kitchen and bathrooms of course.
Materials must be vapour permeable (when installed directly on the masonry) so that they don’t trap moisture. Modern building materials (such as foam insulation boards) don’t breath – it is incredibly complex and hot box situations must be avoided at all costs. Location, orientation, solar gain, moisture and ventilation all have an impact.
Up until recently, Conservation Officers’ standard response to renovations of heritage properties has been very cautious, however this is now having to change out of necessity. Industry experts have forecast a shift in attitude, on account of developments in technology and technique, accompanied by the realisation that change must happen to combat the currently rising climate crisis.
The bottom line is that every building is unique and must be considered as such with the programme of works tailored to suit. Lee explains all of this patiently to me and, coming from him, it makes perfect sense but now, as I revisit my notes that are full of holes (much like a period property) I question my understanding. The process involves a full check list and design matrix. You cannot pick and choose which bits to do and it is also all about sequencing and here, at last, is some better news. If you get the programme and ordering right, the plans can be implemented (and therefore budgeted) over several years… but, you must know what you are doing so that each step is progressive and won’t impact the next step.
Expanding on his theme, Lee goes on to explain that there is so much more to this process than the actual construction. As well as considering sequencing and how these new technologies and methods affect the build process, you must consider the carbon footprint of the build. Everything is affected because it impacts embodied carbon: the carbon in the materials and the carbon used to get materials to and from site. Waste has to be carefully sorted, bagged and, wherever possible, recycled; even the bags used to transport the waste and recycling need to be returned to sites for re-use to limit further carbon emissions. Project managers, trades, labourers and delivery drivers all need to be accounted for – how are they travelling to and from the site and how do you offset it? How many trees do you need to plant? This too all has high cost implications on the project; no longer can you chuck rubbish in a skip and send it to landfill. Everything done is tested and monitored to prove compliance and to get a Pass. There are other standards that are similar to PAS 2035 – BREEAM for example follows the blueprint and whilst it is not certified, it is compliant.
I asked Victoria more about Castellum’s motivation to qualify as a Retrofit Co-ordinator. It generally takes eight months to a year to qualify but Lee got us there in just three months! It is, to date, highly unusual for a building contractor to undertake this qualification (we don’t actually know of any others in the private sector) – it is usually done by Sustainability Consultants specialising in emerging technologies and low energy design and sometimes by forward thinking architects. It transpires that Marion Baeli, an award-winning architect and author who specialises in low energy design and retrofit and is a member of the NLA Net Zero Expert Panel suggested having a senior player within a main contracting company that fully understands this process would give us a huge advantage. Victoria, being Victoria (those that already know her will understand that she is a force to be reckoned with) seized the initiative and is clear that the idea was never for Castellum to be able to design the retrofit packages for the houses we are working on, but, rather, to be able to fully understand the design intent and know how to implement it properly.
Castellum is delighted to reveal that the company has just been appointed by the Grosvenor Estate to update two floors (eight apartments) in Claridge House. The Duke of Westminster is a pioneer in the field of sustainability and well known for his positive stance on it. This project has been carefully planned to enable future upgrades so, whilst only two floors are initially being fully upgraded, the infrastructure (for example pipe sizing) to complete the entire building will also be implemented at this stage.
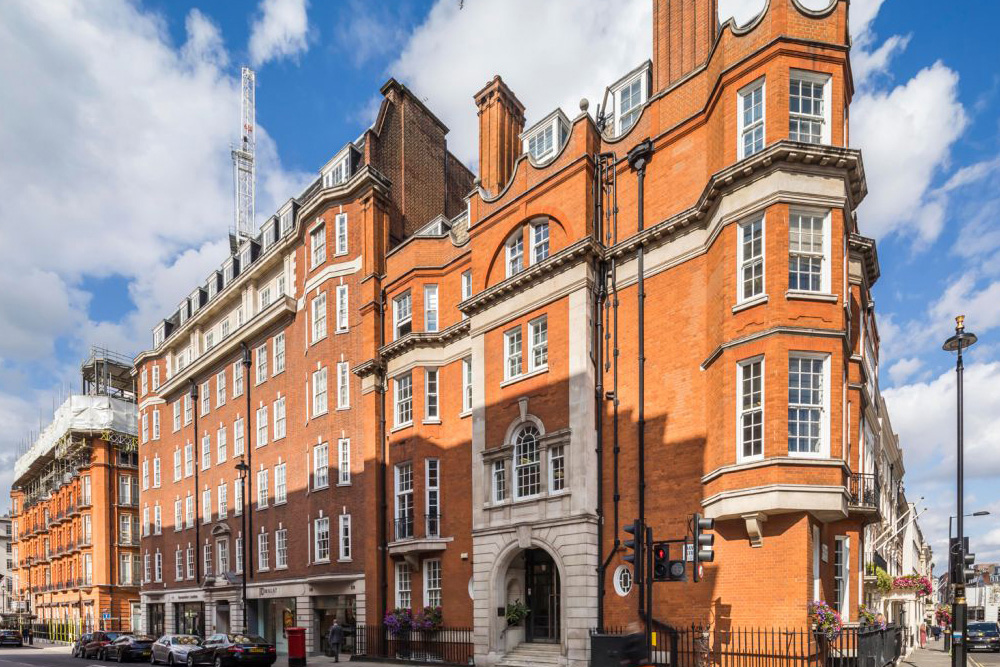
Thankfully The Grosvenor Estate (which has already completed a Net Zero retrofit project) is not alone in leading the way… others too are keen to make a positive early impact, but it will be costly for all property owners and landlords. Not only will they have to budget for the works required to upgrade their dwellings, but they will also have to allow for void periods when the buildings are empty.
I’m slightly aware that I have made much of scale of the challenges ahead generally and I hope I don’t sound defeatist. There is, unequivocally, a great deal to do but you have to start somewhere and I am encouraged that big steps in the right direction are being taken. Successful retrofitting can remove the dilemma between ‘old and beautiful’ or ‘efficient and practical’, thereby securing our architectural heritage for years to come.
Many are commenting on the other obvious potential benefits to a “retrofit boom”. According to an article in The Guardian in March, a new report jointly authored by The National Trust, the housing trust Peabody, Historic England, the Crown Estate and the Grosvenor Estate estimates that the retrofit movement “could generate £35bn of economic output per year, create new jobs and help the government achieve its climate goals”. Retrofitting the UK’s historic buildings will include the obvious Georgian townhouses and country piles, but also the mills and factories that kickstarted the Industrial Revolution. The same article says, in addition, the British Property Federation (BPF) are supporting a “retrofit first” strategy, saying they want the government to introduce an “overarching retrofit strategy and tax incentives”.
“We all have a responsibility to transform the built environment… and we are committed to investing in our team to help deliver this.”
VICTORIA EVANS, MD of CASTELLUM